PIR Foam as LNG Tanks Corner Protection
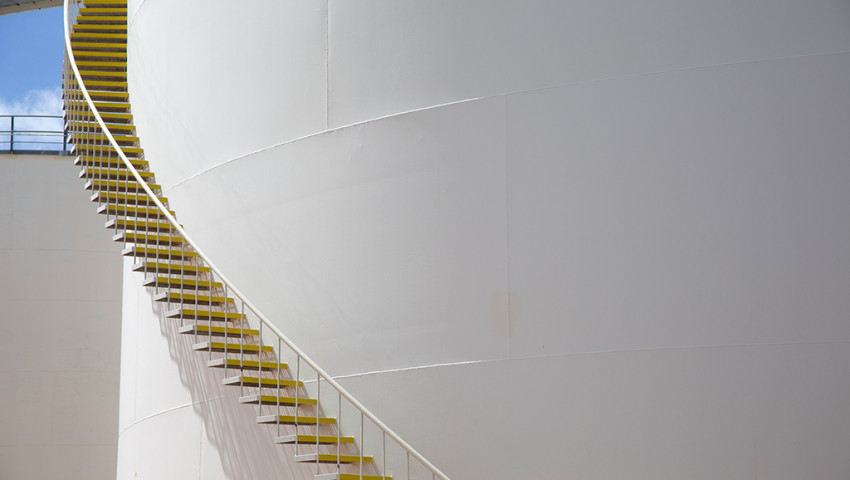
21.11.2013
At almost 50 years from the put in operation of the first LNG plant in the world (GL4Z Arzew - Algeria 1964), it is possible to make significant considerations on technological evolution that has accompanied the awareness and the role of LNG as a viable alternative to traditional energy sources (primarily the oil), starting from the "size" of the production equipment that has been gradually increasing up to the definition of "jumbo Train" introduced in Qatar since 2000.
The strong production growth favored by the fundamental strategic choices of Qatar, Indonesia and Australia, which have heavily invested in new facilities since the early 2000s, resulted in a greater availability of LNG in the world energy market by pushing the parallel race to the improvement of technologies related to this product both in the production and intended use.
The research has focused in particular on the various processes liquefaction plant to increase productivity and on materials which ensure good efficiency of a cryogenic plant, in particular the insulating ones.
Working at a temperature of -162 ° C was from the beginning a powerful discriminator which excluded whole classes of materials traditionally used and made the process of choosing the insulation very selective in favor of high-performing technical materials.
The necessity to operate more and more often on modular systems, built on reduced spaces similar to those of offshore platforms, has further emphasized the selection of high performance insulators, pushing to the maximum technicization of this aspect, which in the past was a little underestimated.
Since always in the field of "cold"insulating materials, DUNA-Corradini was immediately involved in the process of improvement of specific plants when the major engineering companies started to assess the appropriateness of using polyurethane (PUF) and poliisocianurates (PIR) foams instead of traditional inorganic insulating materials already known (mineral wool, perlite, cellular glass, etc..).
Therefore we witnessed directly the progressive critical analysis and subsequent review of the various aspects of the plants in particular, liquefaction plant, jetty lines and tanks.
While the first two aspects have been immediately addressed, coming in a short time to results of great technological value (above all the pre-insulation of Jetty lines made ??by casting and spray systems PIR), with regard to the storage tanks, research of improving solutions has begun in the early 2000s and is still ongoing.
The traditional tank (Land storage tank) is typically double-wall insulated with cellular glass on the bottom and with perlite in the space between the two walls; this gap can measure up to 1000 mm.
A further ring of cellular glass is applied on the outer wall of the tank from the bottom up to a height of 5 meters with a thickness of about 150-200 mm.
This insulation, then covered with metal cladding, provides a containment in case of leaks in the tank in order to have the necessary time to secure the plant (rapid emptying).
The layout of this type of tank remained essentially unchanged until early 2000 when teams of engineers have begun to analyze the technology, never questioned before as functional and reliable, with the aim of making it more convenient and efficient.
Used materials, in fact, especially cellular glass, even if functional, are less efficient from the point of view of the insulation when compared to other products already massively used. Polyurethane foams in particular, supported by increasingly high-tech protective coatings, have gradually replaced the inorganic insulating offering better performance with dimensions (thickness of insulation) and significantly lower costs.
Changing the design of a running system is not easy at all, when the first steps have been made without affecting the drawings and proceeding gradually to replace the materials. Thanks to the close cooperation with DUNA-Corradini, in 2002 the first variant of a Land storage tank has gone on stream.
After an intense campaign of full-scale tests and trials, the first LNG tank with PIR corner protection was then designed and put in place.
The "pioneer" plant was the one in Sines, Portugal for which DUNA-Corradini supplied CORAFOAM® in low density preformed panels ready for installation, as well as the two-component polyurethane adhesive DUNAMIX ™ for fixing the panels to the wall of the tank.
Coated in in correspondence of the welding points with ceramic fiber tissue, the PIR was subsequently coated with metal cladding to obtain a corner protection formally equivalent to the previous one but with the great benefit of a better insulation and therefore greater efficiency in the containment leakage.
The replacement of the material was carried out without changing the size of the protection; despite this, the saving was around the 50%.
Even on a large tank, the corner protection does not affect significantly the cost; however, the success of the operation has opened the way for an in-depth analysis of the entire system including the bottom of the tank, where the glass cell, even if performing very well, is not very versatile in terms of improving performance and remaining substantially equal to itself over time.
Instead, being extremely versatile either alone or associated with mineral fibers to form composites, polyurethane foams seem to be a strong point for a revolutionary LNG containment technology, especially in view of new uses under evaluation.
Particular attention should be given mainly to two classes of new applications: LNG bunkering, that is the use of LNG as fuel on large ships (cruise ships, container ships, etc..) and consequently the construction of small storage facilities along the coasts to supply these"green" low emission vehicles.
They will thus build tanks of small size (miniaturization) to reduce the environmental impact and make them super efficient. Again, insulation will be the center of attention and DUNA-Corradini is already exploring solutions to support the current technological revolution.
Following the design of Sines, many other projects have adpted PIR for the corner protection, these are the main:
- Gate LNG (Netherlands)
- Reganosa LNG and LNG Huelva (Spain)
- Snövit LNG (Norway)
- LNG Skikda (Algeria)